Wind Turbine Maintenance
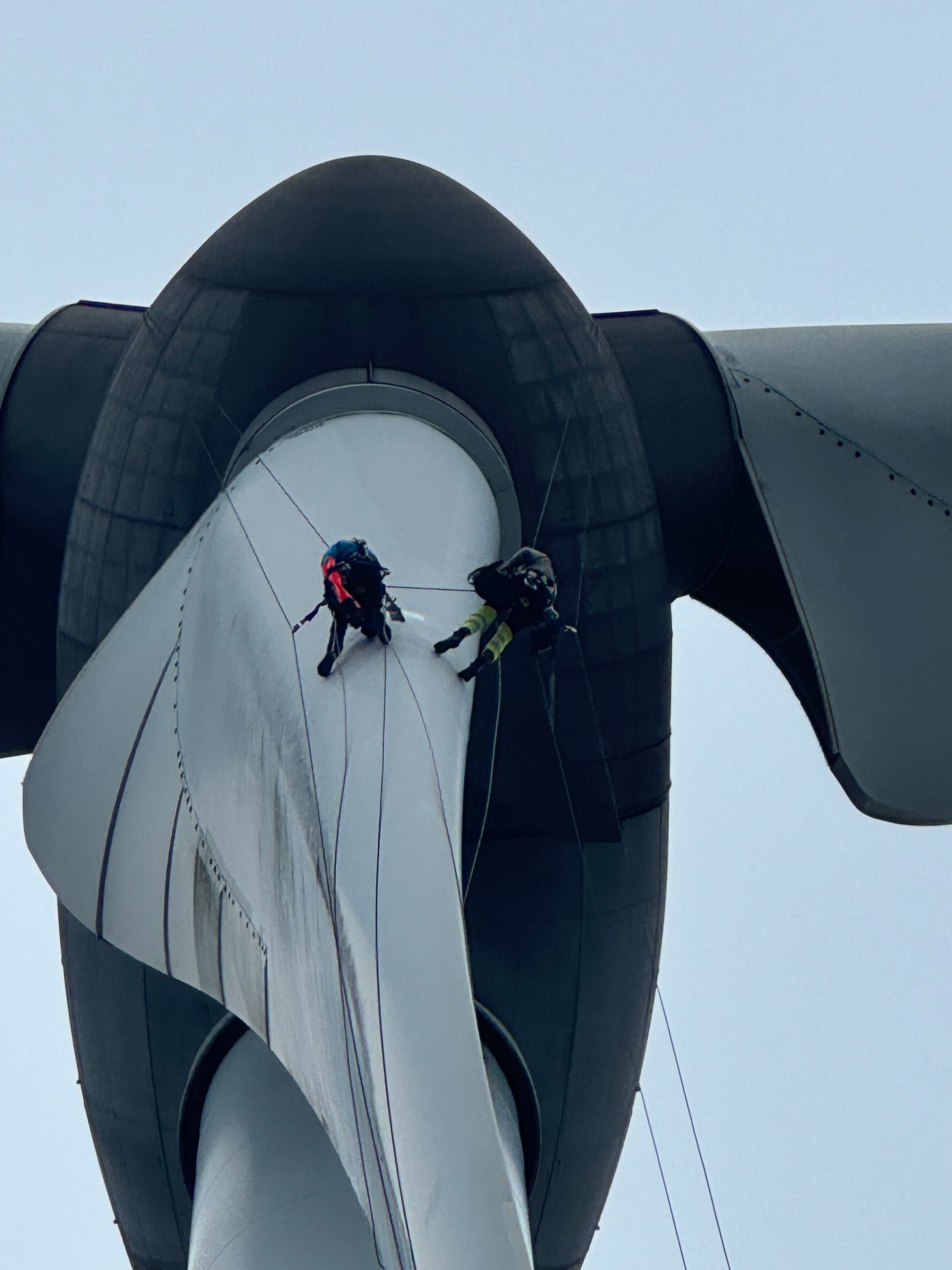
The Ultimate Guide to Wind Turbine Maintenance: Keeping Your Turbines at Peak Performance
Wind turbines are an essential part of the global push towards renewable energy, harnessing the power of the wind to generate clean, sustainable electricity. However, just like any mechanical system, wind turbines require regular maintenance to ensure optimal performance and longevity. Proper upkeep can help prevent costly repairs, reduce downtime, and extend the lifespan of turbines, all while ensuring they continue to operate efficiently and safely.
This comprehensive guide will walk you through the critical steps involved in wind turbine maintenance. Whether you are a wind farm owner, a wind turbine maintenance technician, or simply someone interested in renewable energy, this article is packed with valuable information to help maximise the performance of turbines. At Dangle, we understand the importance of maintaining wind turbines and the crucial role they play in the world’s energy mix.
From inspecting and lubricating components to monitoring performance indicators and conducting regular cleaning, we will cover all the essential tasks required to ensure your turbines remain in top condition. By following expert advice and employing a reliable wind turbine maintenance company like Dangle, you can avoid unexpected breakdowns, increase the lifespan of your turbines, and contribute to a more sustainable future. Let’s dive into the ultimate guide to wind turbine maintenance and discover how to keep these powerful machines running at their best.
Why Wind Turbine Maintenance Matters
Wind turbines are exposed to harsh weather conditions, constant mechanical stress, and the wear-and-tear that comes with continuous operation, 365 days a year. Proper maintenance is critical to ensure that turbines continue to operate efficiently and remain safe. In addition, well-maintained turbines are more reliable, generating electricity more consistently, which is essential to meeting growing energy demands.
Regular maintenance is necessary for the following reasons:
1. Optimised Performance: A well-maintained turbine operates at peak efficiency, ensuring that the energy it generates is maximised.
2. Cost-Effectiveness: Preventative maintenance helps identify issues early, preventing costly repairs or unplanned downtime.
3. Extended Lifespan: Regular care can extend the life of your turbine, delaying the need for expensive replacements.
4. Safety: Proper maintenance ensures that turbines operate safely, reducing the risk of accidents or system failures.
5. Environmental Benefits: Well-maintained turbines contribute to the efficient generation of renewable energy, supporting global sustainability goals.
At Dangle, we believe that regular and proactive maintenance is the key to ensuring that your turbines continue to make a meaningful contribution to clean energy generation.
The Essential Steps of Wind Turbine Maintenance
Routine Wind Turbine Inspections
Regular inspections are the foundation of effective wind turbine maintenance. By carrying out thorough and consistent inspections, you can identify potential issues before they become serious problems. Inspections should be both visual and diagnostic, and may involve a range of techniques from traditional checks to advanced monitoring technologies.
Key areas to inspect on a wind turbine include:
• Blades: Inspect for cracks, erosion, or any signs of damage. Turbine blades are constantly exposed to the elements, so even small imperfections can affect performance and lead to further damage.
• Tower: Check for signs of corrosion, rust, or structural weaknesses. The tower must be in good condition to support the turbine and its flexibility it vital to its integrity.
• Electrical Systems: Look for any signs of wear, such as frayed wiring, exposed cables, or overheating. Electrical systems are critical to the operation of the turbine, so ensuring they remain in good working order is vital.
• Gearbox and Drive Train: The gearbox converts the low-speed, high-torque movement of the blades into high-speed motion for generating electricity. It’s essential to check for oil leaks or wear, as well as ensuring the drive train is aligned and lubricated properly.
• Braking System: Inspect the braking system to ensure it functions effectively, allowing the turbine to stop safely when required.
• Lightening Protection System: Often called the LPS - this system plays a pivotal role in lightening strikes and dispersing the energy from a strike effectively into the ground without damaging the three wind turbine blades.
Inspection Tools:
•
Drones: Drones are used for rapid high resolution imagery to all exterior parts of wind turbine.
• Thermal Cameras: These can help detect overheating components, such as electrical wiring or motor parts, by identifying hotspots.
• Ultrasonic Testing: Ultrasonic waves are used to detect cracks or damage inside turbine components, such as the gearbox or tower using NDT techniques.
• Endoscopes: Small inspection cameras can be inserted into tight areas to check internal parts like the generator, drivetrain or the inside of wind turbine blade, providing a safer and more accurate way to perform inspections.
Wind Turbine Lubrication and Oil Changes
Regular lubrication is crucial to prevent friction and excessive wear in the moving parts of a wind turbine. Components like the gearbox, bearings, yaw and pitch systems all rely on proper lubrication to reduce heat and prevent premature failure.
Lubrication Points:
• Gearbox: The gearbox is one of the most critical components of the turbine. Lubrication reduces friction between gears and bearings, preventing overheating and wear.
• Pitch System: The pitch system adjusts the angle of the blades to optimise energy capture based on wind speed. Regular lubrication ensures that the pitch system operates smoothly.
• Yaw System: The yaw system rotates the turbine to face the wind. Regular lubrication is essential for keeping the system functioning efficiently and reducing the risk of mechanical failure.
Types of Lubricants:
• Synthetic Oils: These oils offer better performance in extreme temperatures and are highly resistant to oxidation, making them ideal for wind turbine use.
• Grease: Grease is often used in areas with less movement, such as bearings, where it provides long-lasting lubrication.
Wind Turbine Monitoring and Diagnostic Systems
With the advent of smart technologies, wind turbine maintenance has become increasingly data-driven. Many modern turbines are equipped with monitoring systems that track performance indicators in real-time, allowing for proactive maintenance and quicker fault detection.
Key Performance Indicators to Monitor:
• Rotor Speed: Rotor speed must be within a specific range to ensure the turbine is generating electricity efficiently. Deviations can indicate problems with the generator or gearbox.
• Vibration Levels: Excessive vibration can be a sign of misalignment in the drivetrain, bearing wear, or blade damage.
• Wind Speed: Monitoring wind speed helps ensure the turbine operates within its safe operating range. The turbine should be able to automatically shut down in high winds to prevent damage.
• Power Output: Keep track of the turbine’s energy production. A drop in power output may indicate an issue with the generator or another critical component.
• Ice Build-up: Dangle have been involved with Ireland's first ever installation of De-Icing sensors which detects ice formation on a wind turbine's blade. Allowing the WTG to be safely stopped to prevent ice being catapulted at high speed from the blades.
Predictive maintenance software can use data from these performance indicators to flag any irregularities and schedule repairs before they lead to failure or injury. This helps reduce unplanned downtime and maintenance costs.
Wind Turbine Blade Maintenance and Repair
The turbine blades are exposed to the elements every day and night, and can suffer from damage due to weather, dirt, or debris. Regular maintenance of the blades is essential to ensuring the turbine operates efficiently and safely.
Blade Maintenance Steps:
• Visual Inspection: Look for cracks, chips, erosion, and other visible signs of damage. The leading edge of the blades is particularly vulnerable to wear.
• Cleaning: Blades can accumulate dirt, debris, and even bird droppings, which can reduce their aerodynamic efficiency. Regular cleaning ensures the blades maintain optimal performance and annual energy performance.
• Repairs: Small cracks or damage can often be repaired using composite materials. However, larger or more serious damage may require replacing the blade or part of the blade.
Most wind turbine operators are now using companies like Dangle for UAV surveys with our drones equipped with high-definition cameras to inspect blades from the ground. This allows for faster and safer inspections without the need for technicians to climb the tower, unless damages are found.
Wind Turbine Cleaning and Dirt Removal
Routine cleaning of wind turbine components is often overlooked, but it plays a crucial role in ensuring efficient operation. Turbines can accumulate debris such as dirt, leaves, bird droppings, and even ice depending on the local environment, which can negatively impact performance.
Cleaning Tasks Include:
• Blades: Regularly remove any accumulated debris from the blades to ensure they remain aerodynamically efficient. This can be done using specialist rope access techniques and cleaning tools or even with the help of drones fitted with large payloads.
• Cooling Systems: Some turbines are equipped with cooling systems to prevent the generator and gearbox from overheating. These systems need to be regularly cleaned to ensure they operate correctly.
• Electrical Components: Dust and dirt can cause electrical components to overheat or fail. Regular cleaning prevents these issues from arising.
Wind Turbine Testing and Calibration
Wind turbines rely on complex control systems that need to be regularly tested and calibrated to ensure proper operation. Over time, these systems can drift or become misaligned, which can impact the performance of the turbine.
Areas to Test and Calibrate:
• Pitch Control: Ensure the pitch system accurately adjusts the blade angle based on wind conditions. Poor calibration can result in inefficiencies or even damage to the blades.
• Yaw Control: Test the yaw system to ensure the turbine is always facing the correct direction relative to the wind. Misalignment can reduce the efficiency of energy capture.
• Brake System: Ensure the braking system functions correctly. Turbines rely on the brake system to stop the blades when needed, particularly during maintenance or high wind conditions.
Wind TurbineTroubleshooting Common Problems
Despite regular maintenance, problems can still arise. Having a solid troubleshooting process in place can help you quickly identify and resolve issues before they lead to more severe damage.
Common Issues Include:
• Electrical Failures: Faulty wiring, inverter malfunctions, or power surges can cause electrical issues that disrupt turbine operation.
• Mechanical Failures: These may include gearbox issues, bearing failure, or damage to the rotor blades.
• Performance Decline: A drop in power output may signal issues with the generator, electrical systems, or mechanical components.
Wind Turbine Safety and Training
Maintaining wind turbines requires specialised knowledge and skills that are essential for the safe and efficient operation of these complex machines. Technicians must undergo extensive training through an approved Global Wind Organisation (GWO) training centre for work at height, first aid and other courses specific to their job, which often involves rigorous safety protocols and the use of specialised equipment. In addition to mastering the technical aspects of handling heavy industry machinery, they must also be prepared to respond swiftly and effectively to potential emergencies, ensuring both their safety and the reliability of the turbines. Therefore, ensuring that your team is properly trained and fully equipped with the necessary tools and knowledge is crucial to maintaining a high level of performance and safety in wind turbine operations. With the right preparation, your technicians can help maximise the efficiency and longevity of these vital renewable energy sources.
Outsourcing Wind Turbine Maintenance to a Specialist Company like Dangle
While routine maintenance can be carried out in-house by trained personnel, many wind farm owners and operators choose to outsource maintenance to specialised companies like Dangle. Outsourcing to a professional maintenance provider offers a number of benefits that can enhance the efficiency, safety, and reliability of your wind turbines.
At Dangle, we recognise the critical role that proper wind turbine maintenance plays in ensuring long-term performance. With years of experience and expertise, we provide tailored services that address the unique needs of each turbine. Below are some of the key advantages of outsourcing wind turbine maintenance to a dedicated service provider like Dangle.
Expert Knowledge and Experience
Wind turbine maintenance is a highly specialised field. It requires extensive knowledge of both mechanical systems and electrical components, as well as the ability to diagnose and troubleshoot complex issues.
By outsourcing to a company like Dangle, you gain access to a team of highly skilled professionals with expertise in maintaining and repairing wind turbines. Our technicians are trained in the latest technologies, tools, and industry standards, allowing us to carry out detailed inspections, maintenance, and repairs quickly and efficiently, all year round.
Dangle’s technicians also stay up to date with advancements in turbine technology, ensuring they are equipped to handle the latest turbine models and systems, from small Vestas V27 wind turbines to the latest, largest and most powerful wind turbines on the planet. This expertise means that you can trust us to deliver high-quality service that meets or exceeds industry standards.
Cost-Effectiveness
Outsourcing maintenance can often be more cost-effective than managing it internally, especially for small to medium-sized wind farms. Running an in-house maintenance team requires investment in equipment, training, and ongoing operational costs.
By partnering with a specialist company like Dangle, you can avoid these expenses. We offer flexible, scalable maintenance contracts that can be tailored to the specific needs of your wind farm. With a service provider like Dangle, you only pay for the services you need, without having to worry about the overheads associated with maintaining a full-time internal team.
Moreover, our proactive maintenance approach helps reduce the likelihood of costly emergency repairs or unscheduled downtime. By addressing issues before they escalate, we help ensure the ongoing efficiency of your turbines, maximising your return on investment.
Reduced Downtime
Wind turbine downtime can have a significant impact on energy production and revenue. Even short periods of downtime can result in substantial financial losses, particularly for large-scale wind farms.
Outsourcing to a maintenance provider like Dangle can help reduce turbine downtime. Our specialists are trained to perform quick, efficient inspections and repairs, often catching issues before they lead to serious breakdowns. Additionally, by utilising advanced diagnostic tools and predictive maintenance software, Dangle can anticipate problems and address them during scheduled maintenance visits, preventing unexpected failures.
Furthermore, with our 24/7 availability for emergency call-outs across Ireland, Dangle can ensure that any issues that arise are dealt with as quickly as possible, minimising any loss of production time.
Safety and Compliance
Wind turbine maintenance is a high-risk activity, and safety should always be the top priority. Technicians need to be skilled in working at height, using specialised equipment, and adhering to strict safety protocols. A company like Dangle has the necessary staff training and certification to ensure that all maintenance work is carried out safely.
At Dangle, we pride ourselves on adhering to the highest safety standards, which are crucial in preventing accidents, protecting workers, and ensuring compliance with industry regulations. We provide comprehensive safety training to all our technicians, ensuring they are equipped to handle the unique challenges that come with maintaining wind turbines.
Additionally, we ensure that all maintenance work complies with the latest environmental and regulatory standards, which is essential for avoiding fines and maintaining certifications.
Flexible Maintenance Plans
Every wind farm is different, with unique operational requirements. At Dangle, we offer flexible maintenance plans that can be tailored to the size, age, and condition of your turbines. Whether you need routine maintenance, emergency repairs, or more advanced predictive maintenance services, we can provide a package that fits your needs.
Our team works with you to develop a maintenance schedule that suits your turbine’s operational conditions. We can also scale our services based on the size of your wind farm, ensuring that you get the right level of service for your investment.
Access to Advanced Technology
Specialist companies like us at Dangle have access to the latest diagnostic tools and technologies to monitor and maintain wind turbines. These technologies include:
• Thermal Imaging: Identifying overheating components that may indicate faults before they cause significant damage.
• Drones: For inspecting turbine blades and other hard-to-reach components, reducing the need for technicians to work at height.
• Predictive Analytics: Using data from sensors and performance monitoring systems, we can predict future issues and carry out preventive maintenance before problems arise.
• Ultrasonic Testing: Utilising Non Destructive Testing (NDT) for detecting internal cracks or wear in turbine components that may not be visible to the naked eye.
By outsourcing maintenance to Dangle, you benefit from access to these advanced tools and technologies, which would otherwise require significant investment in equipment and training if done in-house.
Minimising Operational Impact
Wind turbine maintenance is a time-consuming process, particularly for larger turbines or wind farms. By outsourcing maintenance to Dangle, you can ensure that your turbines are serviced and repaired with minimal disruption to your day-to-day operations. We work around your schedule, ensuring that turbine downtime is kept to a minimum and Annual Energy Output (AEO) is high.
Our team also ensures that any required maintenance is completed in a timely manner, so your turbines can get back to generating power as quickly as possible.
Comprehensive Reporting and Documentation
At Dangle, we provide detailed maintenance reports and documentation to help you track the health and performance of your turbines over time. These reports include information on inspections, repairs, upgrades, and parts replacements, and are invaluable for keeping records of work completed and ensuring that your turbines remain compliant with safety and environmental regulations.
Having detailed records also helps in identifying recurring issues or patterns that may indicate the need for more significant repairs or upgrades in the future. These insights can be critical for long-term planning and budgeting, and they help you stay on top of your turbines’ performance.
The Dangle Difference: A Tailored Approach to Wind Turbine Maintenance in Ireland
At Dangle, we offer a complete range of wind turbine maintenance services, from routine inspections and servicing to emergency repairs and advanced predictive maintenance. We understand the unique challenges faced by wind farm operators in Ireland and across the wider UK are faced with, and we’re committed to providing tailored solutions that keep your turbines running efficiently, safely, and sustainably.
Our team of qualified technicians and support staff works closely with you to design a maintenance schedule that fits your operational needs. Whether you have a small-scale installation or a large wind farm offshore, Dangle offers scalable, flexible solutions that ensure your turbines perform at their best.
Ensuring Optimal Performance with Dangle Wind Turbine Maintenance
Wind turbines are complex and highly specialised machines that require ongoing attention to ensure they perform optimally. Regular inspections, lubrication, cleaning, and repairs are essential to maintaining the efficiency, safety, and longevity of your turbines.
Outsourcing your wind turbine maintenance to a specialist company like Dangle offers numerous benefits, including expert knowledge, cost-effectiveness, reduced downtime, enhanced safety, and access to advanced technology. By partnering with Dangle, you can rest assured that your turbines will be in the hands of professionals who are committed to maintaining the highest standards of service.
Whether you own a small wind farm or manage a large-scale offshore operation, Dangle’s tailored maintenance services will help ensure that your turbines continue to generate clean, renewable energy efficiently, contributing to a more sustainable future for Ireland and beyond.
Why Choose Dangle's Academy?
Here at Dangle, we pride ourselves on offering a wide range of professional and comprehensive inspection, access, coatings, and composite (IACC) industrial services and training courses to cater to the needs of both the private and public sectors. Our dedication to providing high-quality work at height solutions and training has helped us establish a strong reputation in the industry.
With a team of highly skilled and experienced professionals, we are committed to delivering exceptional results that not only meet but exceed our clients' expectations. Our on-site working at height services are designed to minimise maintenance costs in the long and short-term, allowing our clients to save on valuable resources.
Located in Belfast, Northern Ireland, our headquarters serve as the centre of our operations across Ireland. However, we also have a Dangle office based in Scotland, ensuring that we can extend our services to a wider clientele across the United Kingdom. No matter where you are located, our team is always ready to assist you with your industrial maintenance or training needs.
If you would like to learn more about how our dedicated team can help you, we encourage you to get in touch with us today. Our friendly and professional staff are always available to provide you with the information and support you require.
Contact us now to discover the Dangle difference and let us be your trusted partner in meeting your industrial service and training needs today.
We'd Love a Share...
You might also like
