How to Properly Paint Galvanised Steel
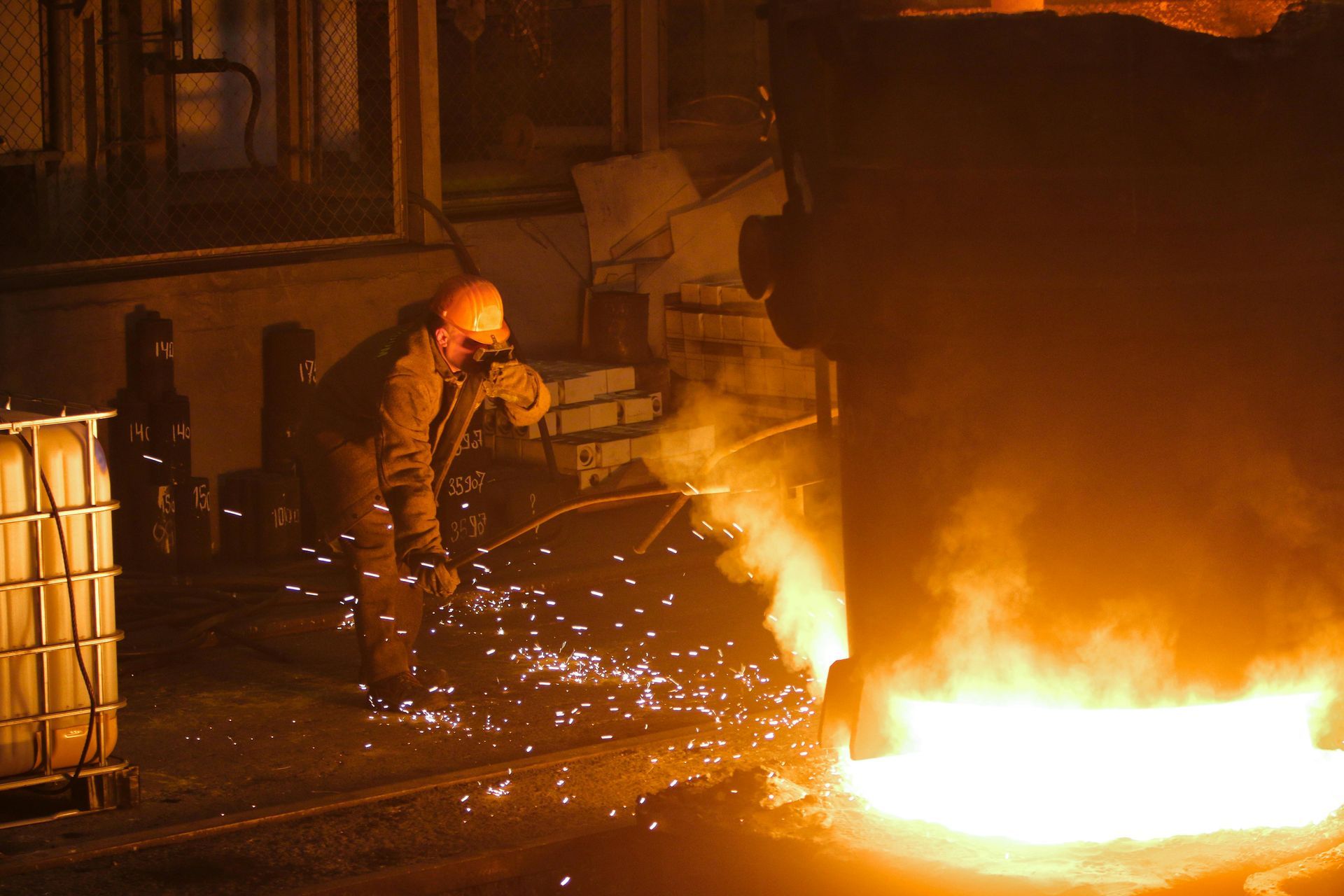
Galvanised Paint for Steel
Advantages of Zinc Paint | Disadvantages of Zinc Paint |
---|---|
Good adhesion to galvanised steel | Can be expensive |
High resistivity to bi-metallic corrosion | Requires proper ventilation when applying due to strong fumes |
Dries quickly | Not suitable for painting bare steel surfaces |
How to Properly Paint Galvanised Steel - Expert Guide
Learn the proper way to paint galvanised steel with our expert guide. Follow these steps for a long-lasting and durable finish that stands up to the elements.
Painting galvanised steel can be a tricky process as it requires a specific approach to ensure the paint adheres properly and lasts . Galvanised steel has a protective layer of zinc coating, and any paint applied directly on it can peel off easily. ISO 12944 is the globally recognised standard for the corrosion protection of steel structures by protective paint systems.
With our expert guidance, you'll learn everything you need to know about how to properly paint galvanised steel, from understanding the material to curing and maintaining painted galvanised steel. Read on to discover the best techniques for painting galvanised steel and get your job done right, first time, as re-work is even more costly!
Painting Galvanised Steel
Painting galvanised steel is simply a type of steel coated in a layer of zinc to protect it from corrosion. This coating creates a barrier that prevents the steel from coming into contact with moisture and oxygen over time, which are the two primary causes of corrosion. While galvanised steel is somewhat resistant to corrosion, it is still susceptible to bi-metallic corrosion when it comes into contact with bare steel or other metals.
Bi-metallic corrosion occurs when two dissimilar metals come into contact with each other in the presence of moisture and oxygen. When this happens, an electrochemical reaction takes place, which causes one of the metals to corrode faster than normal, this is often called a "anode". In the case of galvanised steel, if it comes into contact with bare steel, the zinc coating will corrode faster than it normally would, leaving the steel vulnerable to corrosion, unless expert advice is sort.
Understanding Galvanised Steel and Bi-Metallic Corrosion
In order to prevent bi-metallic corrosion, it is important to use the proper isolation methods when working with galvanised steel. This can include using gaskets or washers made from materials like rubber or nylon, that are compatible with both the galvanised steel and the other metal it will come into contact with. It is also important to avoid leaving any bare steel exposed when working with galvanised steel, as this can create a direct path for bi-metallic corrosion to occur.
Tip: When working with galvanised steel, it is a good idea to use tools, fasteners, and other materials that are specifically designed for use with galvanised steel, as these will be less likely to cause bi-metallic corrosion.
It is also important to note that while galvanised steel is partly resistant to corrosion, it is not completely immune. Over time, the zinc coating can wear away, leaving the steel vulnerable to corrosion. For this reason, it is important to monitor galvanised steel for signs of wear and damage and to address any issues as soon as possible to prevent corrosion from occurring.
Note: If you are unsure about the condition of your galvanised steel or how to properly maintain it, it is always best to consult with a professional industrial painting company, like Dangle to ensure that your steel is properly protected.
Painting Newly Galvanised Steel
The process of painting newly galvanised steel, is similar to that of aged galvanised steel, so it is important to properly prepare the surface first as you would with any substrate. Failure to do so could result in poor adhesion and premature paint failure, leading to costly rework and maintenance.
It is essential to remove any contaminants, including oil, grease, and dirt, from the surface. This can be accomplished using a mild detergent or solvent and a soft-bristled brush or sponge. Rinse thoroughly with clean water and allow the steel to dry completely.
Next, inspect the surface for any defects, such as rough spots and sharp edges. Surface imperfections are usually defined in ISO 8501-3 with a rounding of sharp edges to no less than 2mm. Uneven surface imperfections should be smoothed out using a suitable power tool like a grinder or a wire brush to ensure an even surface before painting.
It is also important to consider the age and condition of the galvanised coating if not newly galvanised. If the steel has been exposed to the elements for an extended period of time, the zinc coating may have oxidised or developed a white powdery film known as "white rust." This must be removed using a chemical or mechanical treatment prior to painting, if not the paint will not adhere correctly and eventually peel off.
Consult with our professional industrial painters for the best course of action.
Finally, it is recommended to use a high-quality primer specifically designed for galvanised steel. This will enhance adhesion and help mitigate corrosion. Always follow the manufacturer's instructions for the best results.
Choosing the Right Paint for Galvanised Steel
Choosing the right paint for galvanised steel is crucial to ensure maximum longevity of the painting job. Not all paints work for galvanised steel, and selecting the wrong paint can lead to early peeling and flaking.
The ideal type of paint for galvanised steel is zinc paint. Zinc paint is epoxy-based and has a high resistivity to bi-metallic corrosion, which occurs due to the presence of bare mild steel in close proximity to the galvanised steel.
Zinc paint also has good adhesion properties, which helps in ensuring the paint sticks firmly to the galvanised steel surface.
It is important to note that other types of paint, such as oil-based or acrylic paints, are not recommended for galvanised steel painting. These paints can lead to peeling or flaking of the paint layer due to poor adhesion to the galvanised surface no matter how well the surface prepared.
When choosing the right paint for galvanised steel, it is also important to select a paint that matches the intended use of the painted steel. For example, if the painted steel will be exposed to harsh weather conditions, it is recommended to choose a paint that has a high UV resistance. The selection of coating systems is also defined in ISO 12944-2 and ISO 12944-5.
Paint for Galvanised Steel
Now that the galvanised steel has been properly cleaned and prepared, and the right paint has been chosen, it is time to apply the paint to the galvanised steel. Follow these steps to ensure an even and long-lasting coating:
- Apply the paint in thin coats using a brush, roller, or spray gun. It is better to apply several thin coats than one thick coat, as thick coats can result in drips, sags, and an uneven finish, as well as increasing the curing time.
- Allow each coat to dry completely before applying the next. The drying time will depend on the type of paint and the temperature and humidity of the environment. Check with the paint manufactures technical data for specific instructions.
- If necessary, lightly sand the surface between coats to ensure optimal adhesion, if not you really rely on a process called chemical cohesion, which in simple terms is the chemical bonding of the two coats of paint.
- Avoid painting in direct sunlight or when the surface is hot to the touch, as this can cause the paint to dry too quickly and result in a poor finish, with coating defects likely to occur.
- Use a high-quality brush or roller to avoid leaving brush marks or roller sleeve stipple. If using a spray gun, follow the manufacturer's instructions for use and maintenance.
- Apply enough paint to cover the surface completely, but avoid overworking the paint, as this can result in brush marks, roller sleeve stipple, or an uneven finish.
- Repeat the process until the desired number of coats has been applied. In general, two to three coats are sufficient for most applications, however always follow the coating specification and manufactures technical data sheets.
Note: Remember to use caution when working with paint, especially when using a spray gun. Wear protective clothing and a respirator if necessary, and take appropriate safety measures to avoid inhalation, ingestion, or contact with skin and eyes.
"Applying paint to galvanised steel requires patience and attention to detail. Take your time and follow the manufacturer's instructions for the best results." - Simon, Industrial Painting Expert & Author
Maintaining Painted Galvanised Steel
After painting galvanised steel, it is vital to allow the paint to cure properly. This ensures that the paint adheres to the steel surface and provides long-lasting protection against corrosion and other forms of damage.
Typically, curing time for paint on galvanised steel ranges from 24 to 48 hours. However, the exact curing time may vary depending on the type of paint used and environmental conditions such as temperature and humidity. It is crucial to follow the manufacturer's instructions for curing time to achieve the best results.
Proper maintenance for painted galvanised steel
After curing, the painted galvanised steel requires proper maintenance to ensure it remains in good condition. Regular cleaning and inspection can help to identify any defects or issues that may arise.
When cleaning painted galvanised steel, take care to avoid harsh chemicals or abrasive materials that may scratch or damage the surface. Instead, use a soft cloth or sponge with mild soap and water to gently clean the surface. It is also essential to avoid using high-pressure water jets or steam cleaning, which can damage the paint and expose the steel to corrosion.
Inspect the painted galvanised steel regularly for signs of damage, including peeling, cracking or rusting. Promptly address any issues to prevent further damage and ensure the steel continues to provide optimal coating protection.
Benefits of properly curing and maintaining painted galvanised steel
By properly curing and maintaining painted galvanised steel, you can enjoy a range of benefits, including:
- Long-lasting protection against corrosion and other forms of damage
- Cost savings by avoiding the need for frequent maintenance or replacement of damaged or worn steel
- Enhanced aesthetics for a more professional appearance
Proper maintenance of painted galvanised steel is crucial for ensuring optimal performance and longevity. By following the manufacturer's instructions for curing time and regularly cleaning and inspecting the surface, you can enjoy long-lasting protection against corrosion and other forms of damage.
Common Mistakes to Avoid when Painting Galvanised Steel
Painting galvanised steel requires special attention to detail to ensure a long-lasting and durable finish. However, there are several common mistakes that can undermine your efforts and lead to disappointing results.
Here are some pit-fall things to avoid:
Skipping preparation - Newly galvanised steel requires thorough cleaning and preparation before painting to remove any surface contaminants that can interfere with paint adhesion.
Using the wrong type of paint - Zinc paint is recommended for painting galvanised steel because it is designed to adhere to zinc-coated surfaces. Using a different type of paint can result in poor adhesion and premature peeling.
Overlooking bi-metallic corrosion - If galvanised steel comes into contact with bare steel or other metals, bi-metallic corrosion can occur. This can undermine the integrity of the paint and lead to rust formation.
Not allowing sufficient drying time - Paint needs adequate time to dry before curing. Rushing the process can cause the paint to bubble, crack, or peel prematurely. Always consult with the paint manufactures technical data sheet.
Applying too thin or too thick a coat - Failure to apply paint evenly can lead to an unattractive finish and poor adhesion. Applying too thin a coat can also result in inadequate protection, while applying too thick a coat can cause the paint to crack or peel.
By avoiding these common mistakes, you can help ensure that your painted galvanised steel surfaces look great and provide long-lasting protection against corrosion and wear.
Benefits of Hiring Professional Industrial Painters
While painting galvanised steel may seem like a simple task, it requires expertise and experience to ensure a long-lasting, quality finish. Hiring professional industrial painters from Dangle for your galvanised painting needs comes with several benefits:
- Expertise: Professional industrial painters that have the knowledge and skills to properly prepare and paint galvanised steel, ensuring the finish is durable and resistant to corrosion.
- Efficiency: With specialised tools and techniques, our professional industrial painters work quickly and efficiently, minimising downtime for your business.
- Quality Results: Dangles professional industrial painters use top-quality paints and coatings, ensuring a smooth and even finish that will last for years to come.
- Safety: Industrial painting can be dangerous, with hazards such as fumes and working at heights. Professional painters are trained to follow safety protocols and have the necessary equipment to minimise risk.
- Cost Savings: While it may seem more expensive upfront to hire our professional industrial painters, their expertise and efficiency can actually save you money in the long run by ensuring a long-lasting finish that won't require frequent touch-ups or repairs.
When searching for a professional industrial painting company, be sure to choose one with experience in painting galvanised steel and a reputation for quality, safety and training.
Why Choose Dangle's Academy
Here at Dangle, we pride ourselves on offering a wide range of professional and comprehensive inspection, access, coatings, and composite (IACC) industrial services and training courses to cater to the needs of both the private and public sectors. Our dedication to providing high-quality work at height solutions and training has helped us establish a strong reputation in the industry.
With a team of highly skilled and experienced professionals, we are committed to delivering exceptional results that not only meet but exceed our clients' expectations. Our on-site working at height services are designed to minimise maintenance costs in the long and short-term, allowing our clients to save on valuable resources.
Located in Belfast, Northern Ireland, our headquarters serve as the centre of our operations across Ireland. However, we also have a Dangle office based in Scotland, ensuring that we can extend our services to a wider clientele across the United Kingdom. No matter where you are located, our team is always ready to assist you with your industrial maintenance or training needs.
If you would like to learn more about how our dedicated team can help you, we encourage you to get in touch with us today. Our friendly and professional staff are always available to provide you with the information and support you require.
Contact us now to discover the Dangle difference and let us be your trusted partner in meeting your industrial service and training needs today.
FAQ
We'd Love a Share...
You might also like
